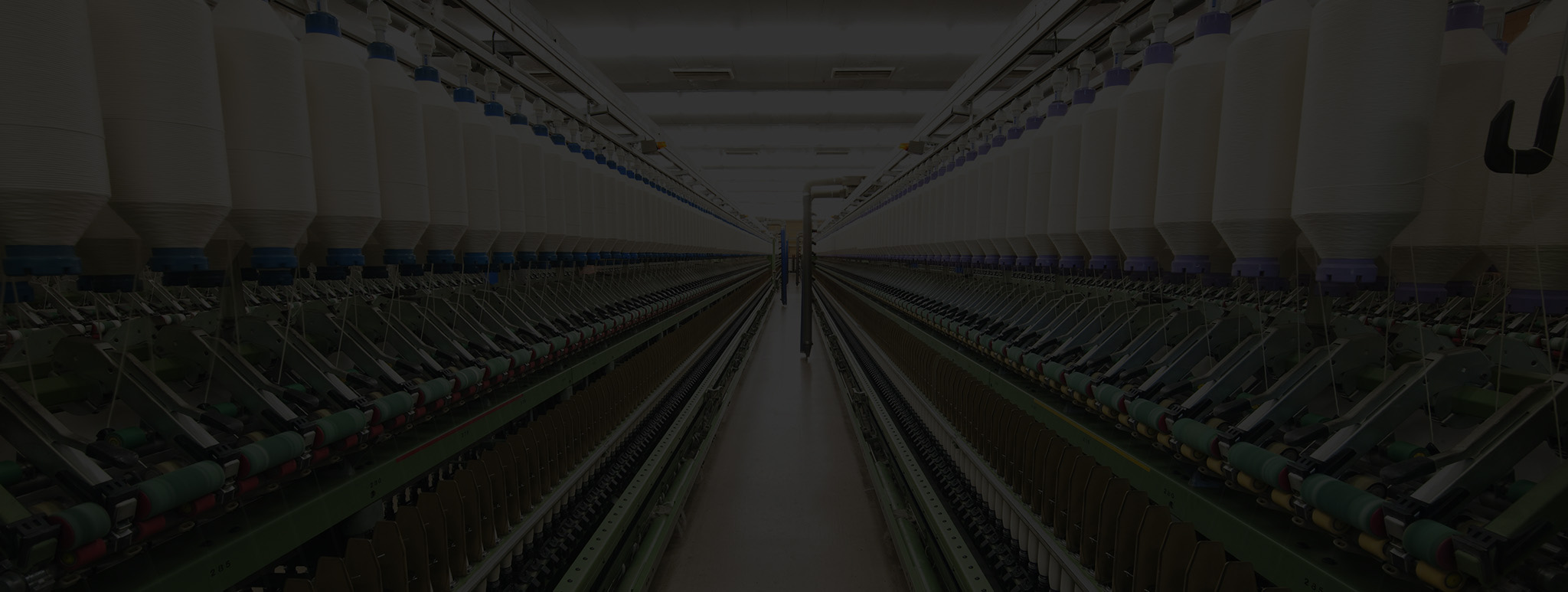
Can lubricants help reduce excess energy consumption in ‘Ring-frame machines?
June 26, 2021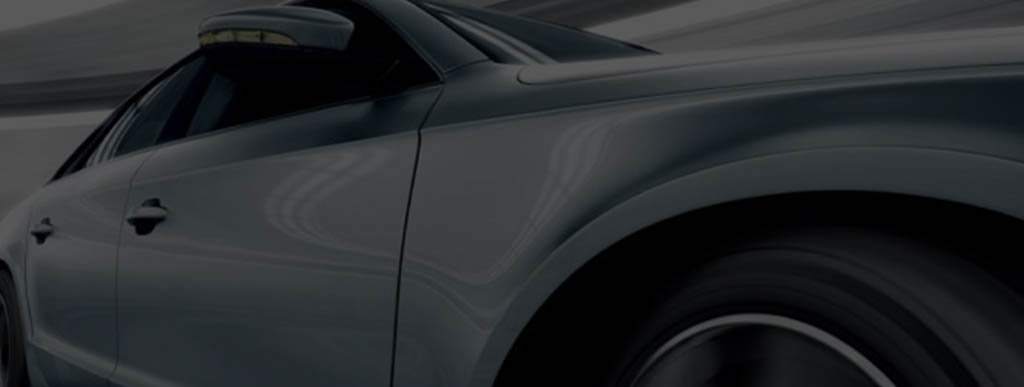
How can dry film lubricants affect performance of automotive components?
February 4, 2022Effect of drawing oil on production efficiency in bright bar drawing process
Can quality of drawing oil improve production efficiency in bright bar drawing process ?
In Bright bar drawing process, extreme surface pressure and specific frictional forces are critical aspects that can affect tool life and workpiece finish. Typical challenges for manufacturers include dull finish of drawn bars, frequent die wear, cracks or even breakage in drawn products. Traditionally use of conventional oil or even mustard oil with suboptimum viscosities has often led to multiple complications resulting in production down time. The drawing oil plays a key role in increasing production efficiencies for manufacturers.
Beruform MF 155 I is recommended for the critical stage of ‘deep drawing’ in the bar drawing process. The multifunctional drawing oil has the right viscosity and advanced additive package that ensures superior surface finish of the drawn bar, longer die life and extended oil service life.
Case Study: Customer experiences 3X increase in Oil Sump Life, die polishing interval extended to 24X
Customer: A reputed manufacturer of steel and special alloy bars with supplies to diverse industries including automotive, engineering, bearing and allied industries. The company has an advanced manufacturing set-up with extensive use of automation for the production process. The company supplies to the top brands in the automotive and heavy engineering industry and has its processes and environmental practices certified to the standards of ISO and IATF.
With an annual capacity to produce 24,000 MT of bright bars, the company managed the shift round the clock to meet the market requirement. Any downtime meant additional pressures on the production team to meet the targets.
Product: | Bright bar steel of various shapes |
Grade: | Plain carbon steel to high alloyed steel |
Size: | 16 mm to 120 mm for round bar 19.5 mm to 40.5 mm hexagonal bar |

Current drawing oil: Mustard oil was in use during cold drawing process of steel bar
Issues faced:
- Frequent die polishing, almost in every three hours resulting in regular production breaks
- Frequent machine suspension and production downtime due to clogging of machine elements
- Oil was changed every 15 days
Considering the operational parameters and Customer’s concern of frequent production downtime, Bechem’s Application Engineering team recommended Beruform MF 155 I.
‘Beruform MF 155 I’ is a non-water-miscible multifunctional oil, specially formulated to provide optimum lubrication between work piece and tool by reducing friction, heat and wear, thereby extending tool/ die life and ensuring high quality formed products.
Benefits of Beruform MF 155 I as bar drawing oil
- Efficient production: ‘Beruform MF 155 I’ provides excellent lubricity during high speed bar drawing process and prevents defects and surface cracks on drawn bars
- Prolonged die life: ‘Beruform MF 155 I’ forms a strong lubricating film and prevents metal to metal contact under the high-pressure operating environments, reducing wear and thereby extending die life
- Optimal viscosity: With a viscosity range of 99 to 120 cSt 40 °C, Beruform MF 155 I has been developed to deliver effective lubrication to the application with excellent pumpability and flow characteristics.
- Optimum consumption: ‘Beruform MF 155 I’ has low evaporation loss and retains its viscosity characteristics for longer durations and thereby extends re-lubrication interval
- Bright surface finish: Ensures uniform shape and size of the drawn bars with bright and smooth surface finish
- High productivity: Residual films left on the parts do not interfere with subsequent operations
- Versatile: Recommended for drawing of round bars and profiles (square, hexagon etc.) with difficult geometries. Suitable for alloy steel and stainless steel
- Forming degrees between 20% to 30% can be easily achieved
Trial Observation:
- Die polishing interval extended from 3 hours to 3 days
- Smooth operation with no machine failure and production downtime during trial period of 45 days
- Congestion of machine components was not observed during the trial period with regular operating conditions
- Sump life extended up to 45 days.
- Reduced rejection rate significantly as the Production team was able to produce parts with uniform shape and size with superior surface finish
- Significant improvement on cleanliness of the drawn bar

Result:
Having observed performance of the product and increase in production efficiency during the trial period, the satisfied customer switched over to ‘Beruform MF 155 I’ completely. Further, the safety quotient of the work environment improved significantly with minimum man and machine interference.
Why “Beruform MF 155 I”
- Formulated on high quality base oils with optimum viscosity for superior lubrication and longer service life
- Comprehensive anti-wear and extreme pressure additive package extends die life in spite of high loads
- Has low evaporation rate. Residual oil film on dies and workpiece provides intermediate rust protection
- Provides for flexible application process
- Has good rinsing properties thereby ensures hassle free cleaning
- Free from Chlorine and other heavy metals
Beruform MF 155 I is also recommended as ‘multi-function’ oil for the processes of blanking, punching and deep drawing. The product has provided superior results in forming of automotive components such as clutch cover body, keys, exhaust shell etc. Other interesting components where Beruform MF 155 I has proven its performance as well as cost benefits include blanking of bearing cages, deep drawing of cylinders etc.
Beruform MF 155 I is compatible with both ferrous and nonferrous metals like steel, stainless steel, aluminium, copper, brass etc. An iteration of the product with Chlorine additives named, Beruform MF 155 C is also available for severe bar drawing operations.
For more information on Bechem’s Cold forming oil range, technical comparison, case studies and references, drop in a query or mail us on [email protected]. We will connect you with our product specialist.