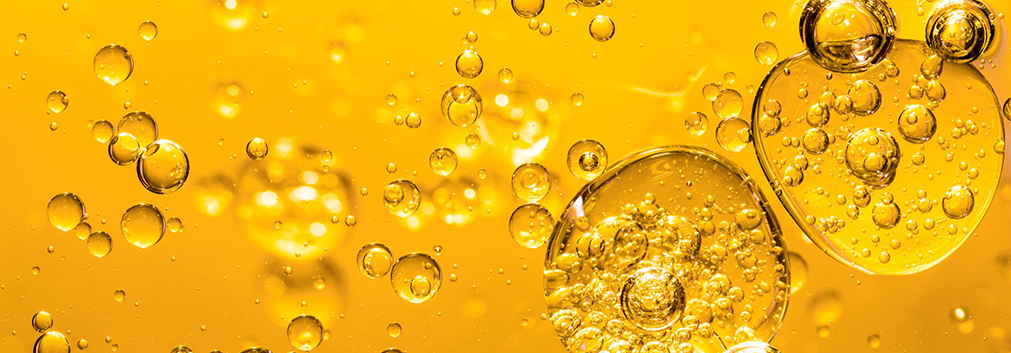
Advanced neat oils for productivity and cleaner work environment
May 12, 2023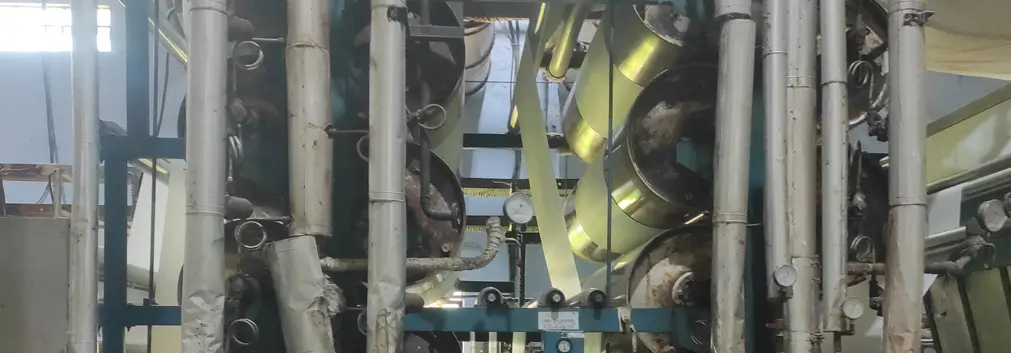
Challenges in lubrication of bearings exposed to high temperatures.
September 25, 2023A case study on effectiveness of MQL for drilling operation.
Drilling as a machining process is often considered a challenging process due to multiple factors such as strain hardening, toughness, high plasticity, tendency to form built-up edges and difficulty in chip evacuation. The role of cutting fluid is indispensable to reduce both temperature as well as friction between chips and the drill flutes and additionally to clear off the hot chip debris. However, the conventional ‘flood lubrication’ process typically used for lubrication, cooling and chip evacuation, often trigger issues like frequent re-lubrication, abrupt tool wear, disposal of used coolant etc.
Among other lubricant application techniques, the process of spraying out limited quantity of cutting fluid as cold mist to the cutting zone has proved to be effective. With MQL, there is minimal or no need to clean the tool and workpiece regularly after every machining process. Additionally, the task of disposal of used medium gets eliminated completely.
Can the process of Minimum Quantity Lubrication (MQL) reduce operational costs in metal drilling processes?
Customer: A leading Indian manufacturer with over four decades of experience in manufacturing forged engine and drive-line components. The technology driven company with multiple production facilities caters to the automotive, earth moving, tractor and pipe fitting industries across the globe.
Machining Parameters
Application: Pin hole drilling
Machine type: Oil hole machine
Machine OE: Reputed Indian brand
Material: Steel
Existing cutting fluid type: Mineral, OE recommended
Viscosity at 40˚C: 47 mm²/S
Pressure- 3-4 bar
Customer was using OE recommended non-water miscible oil, brand “X” for over seven years. During this phase the customer with an intention to reduce operational cost had conducted multiple trials with alternate cutting fluid brands available in the market. However, none of the trials were successful due to concerns of tool life and machining performance.
Consequently, when approached by BECHEM’s Engineering team, the Customer was skeptical. Nevertheless, the team convinced the customer for a trial opportunity for its MQL product, Beruform STO 110.
Trial observation:
- Superior machining performance
- Consumption of 2 litres of Beruform STO 110 observed for a span of 10 days. No operational downtime.
- Over 40% reduction in cost per component with Beruform STO 110 when compared to the existing product
Why Beruform STO 110?
The next generation of Bechem MQL lubricants have been specifically formulated to solve existing problems of wet machining with performance and productivity.
- Developed from high performance synthetic base oils
- Beruform STO110 ensures less smoke and mist formation and hence ensures work friendly environment for the operator
- Beruform STO 110 as an MQL facilitates near-dry machining with superior machining results and a cleaner workplace
- Beruform STO 110 is free from heavy metal containing additives like Chlorine, Sulphur etc. and ensures a safer work environment and hassle-free disposal.
For more information on BECHEM’s mist oil range and to experience reliable and cost-effective MQL solutions, write to us at [email protected].