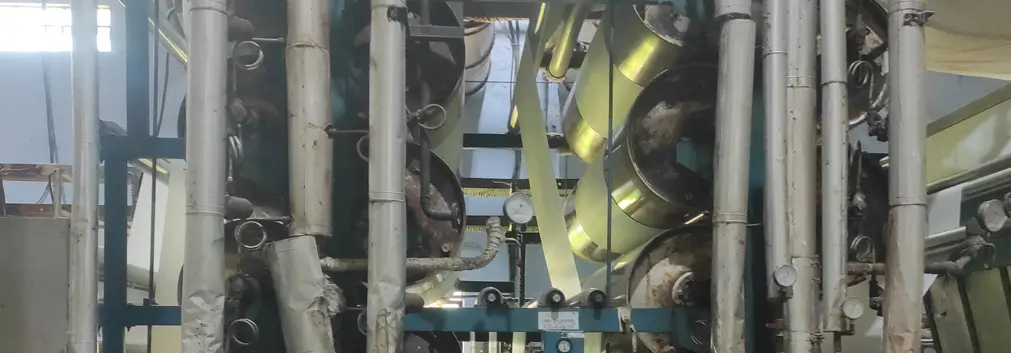
Challenges in lubrication of bearings exposed to high temperatures.
September 25, 2023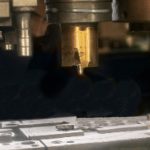
High Performance Grease for Effective Lubrication of Forging Press
March 12, 2024Enhancing operational reliability of Vertical shaft impactor (VSI) crushers with effective lubrication
Vertical shaft impactor (VSI) crushers, widely used in the construction and mining industries, are uniquely designed for high-impact crushing. The crushers are suitable for a wide range of applications including the production of high-quality manufactured sand, well-formed aggregates, and industrial minerals.
Working Principle of Vertical Shaft Impactor (VSI) Machine
- The principle involves a fast-spinning rotor that is fed with the solid hard stones (mostly boulders or granite) by conveyor mechanism. The centrifugal forces generated by the rotor, throw the stones at high speeds against a solid stationery impact wall. The impact causes the material to shatter into smaller pieces due to their natural fault lines.
- The rotor with shaft and bearing are connected to drive pulley mechanism. Due to different size and shape of the stones being processed, the operating conditions induce impact loads and vibration in bearings of the rotor.
- Even though the sealing is effective, the abrasive nature of the dust particles can cause cracks or ruptures in seals over time, resulting in the entry of fine dust particles into the bearing and cause damage.
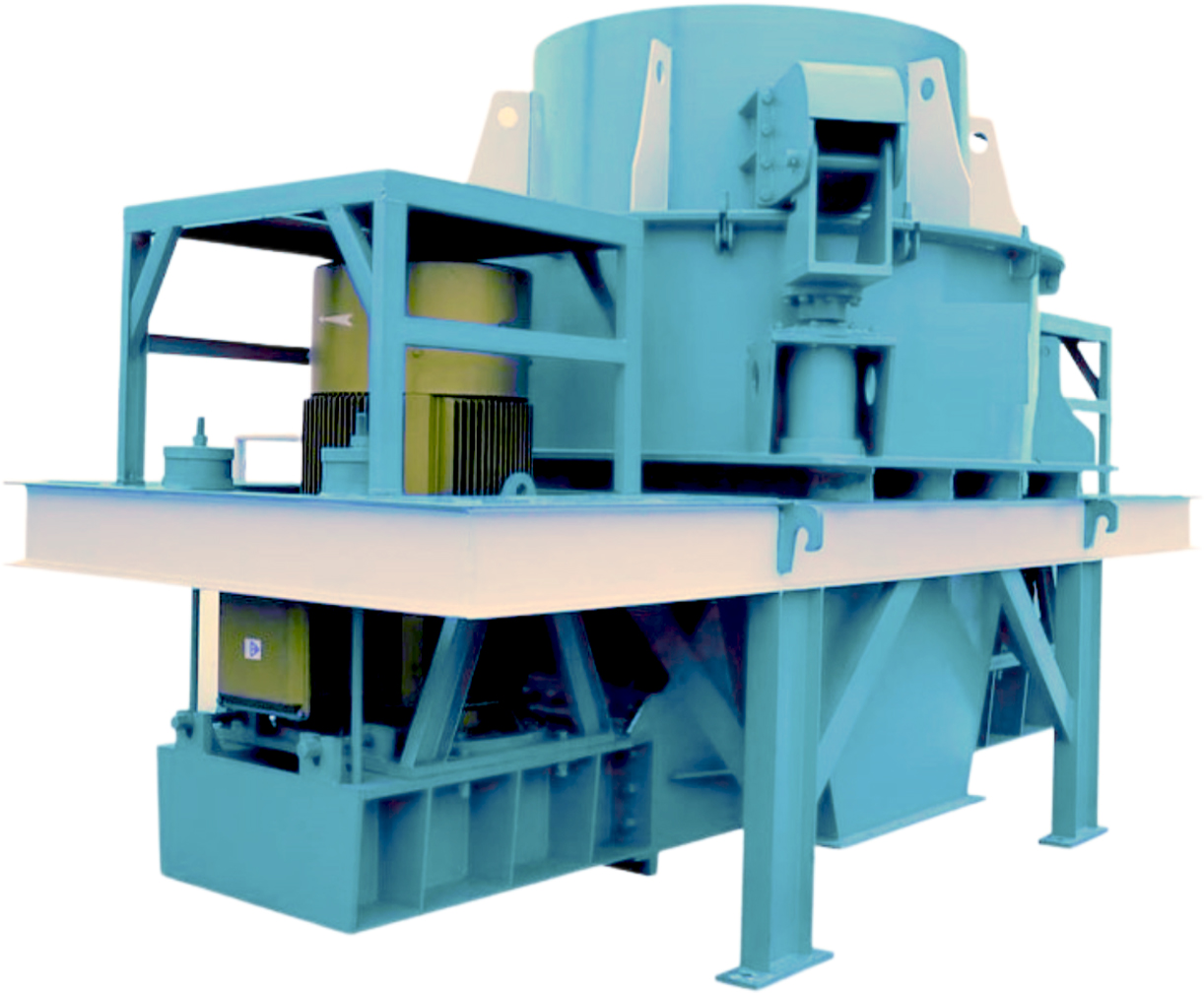
Vertical Shaft Impactor (VSI) Machine
Common reasons for premature bearing failures in VSI Crushers:
- Contamination of lubricant inside the bearing with abrasive wear and debris
- Selection of grease with incorrect base oil viscosity and viscosity index for the application
- Temperature and consistency behaviour of the grease
- Fretting or fretting corrosion, which typically results from a loose fit of bearing inside housing or shaft, leading to relative motion between the bearing and the shaft or housing
- Incorrect lubrication practices such as over lubricating the bearing leading to excessive heat build-up.
Spherical or cylindrical roller bearings used in the assembly require proper lubrication in order to dissipate heat, prevent friction and minimize wear. The formation of an effective hydrodynamic lubrication film on the rolling surfaces prolongs the bearing fatigue life. Selection of a high-quality lubricant to perform in such a challenging operating environment, is crucial to optimize equipment performance while reducing the risk of failure.
The below case study demonstrates how lubricants can play a crucial role in enhancing reliability of VSI machines in the face of harsh operating conditions.
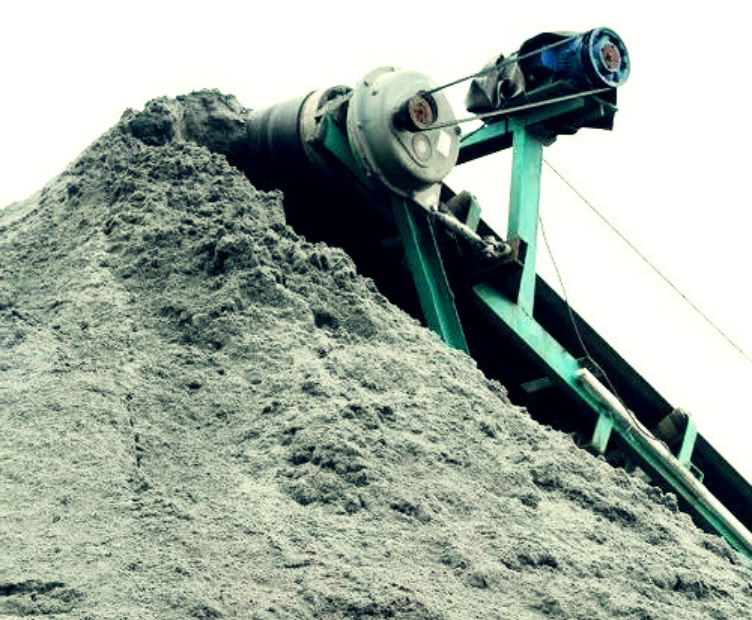
Manufactured Sand
Customer: A renowned manufacturer of ‘Manufactured sand or popularly known as M sand’ in the Southern region of India, with an installed capacity of 3200 Tons/day and supplies to leading construction companies across the region.
Operating conditions of the bearings in Vertical shaft Impactor:
- Bearing position: Vertically mounted
- Bearing number: NU 2324/QJ 2324
- Bearing type: Cylindrical roller bearings
- Bearing RPM: 1500
- Operating temperature: 110˚C
- Dust entry: M Sand dust particles
- Frequency of lubrication: Once in 8 hours
Challenges encountered by the production team:
- High operating temperatures of 80°C to ≥ 120°C resulted in rapid degradation of lubricant, leading to insufficient lubrication and frequent bearing failures.
- Frequent relubrication cycles (every 8 hours) made it difficult for continuous production
- The maximum production output was only 2000 Tons/day
- Frequent replenishment of lubricants results in increased operational costs
- Vertically mounted bearings caused additional challenges. Increase in centrifugal forces during operation, lead to rise in churning losses of grease in the bearing along with the influence of gravitational forces.
The customer was using a mineral oil-based grease of a reputed brand and was in search of an alternate to maximize production capacity while reducing operation costs.
Considering round-the-clock (24/7) operations, BECHEM’s engineering team recommended Beruplex LIEP 3, specially designed for vertically mounted bearings, fortified with an additive package for absorbing shock loads and vibration.
Why Beruplex LIEP 3?
- Developed on optimum -viscosity base oil, Beruplex LIEP 3 forms an effective lubrication film on the cylindrical roller bearings used in VSI machines and provides continual protection from wear.
- Beruplex LIEP 3 ensures superior adhesion on bearings due to the polar nature of the lithium-complex thickener, which is ideally suited for bearings rotating at high speeds.
- Excellent structural stability provided to Beruplex LIEP 3 for mechanisms exposed to shock loads and vibrations.
- Additive package in Beruplex LIEP 3 protects bearings from high friction zones especially during start-up and shut-down phase.
- Also provides effective protection against corrosion
- Beruplex LIEP 3 is a NLGI 3 grade grease which provides essential stiffness in vertically mounted bearings.
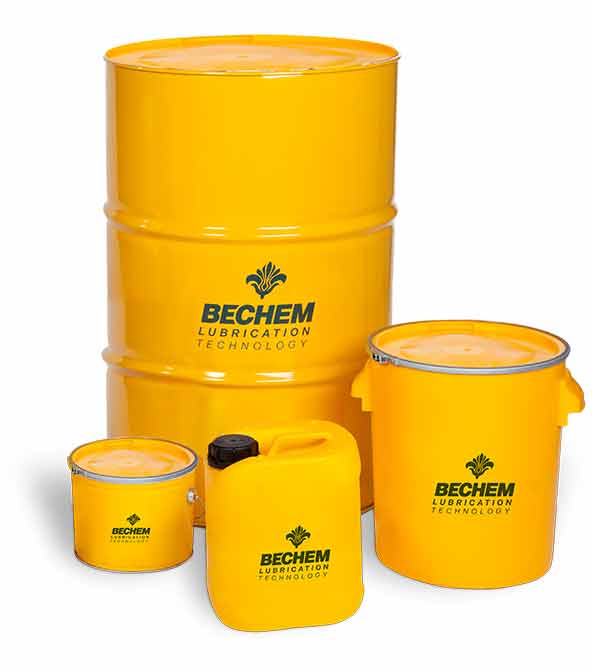
Trial Observations:
- Smooth operation with minimum bearing failure during the trial period. Also, machine run-time was enhanced.
- The frequency of re-lubrication extended from 8 hours to 24 hours.
- Prolonged re-lubrication intervals reduced frequent man-machine interference.
- Better lubricity reduced grease leakage and ensured a cleaner work environment.
- Reduction in lubricating quantities with Beruplex LIEP3 benefitted the customer commercially as well.
Having observed the performance during the trial period, the customer was convinced of the reduction in grease consumption, resulting in cost saving and has since switched over to Beruplex LIEP 3.
For more details on Beruplex LIEP 3 sample of the product, write to us at [email protected]
Support response: Median email response time of less than 3 hours.
You May Be Interested In
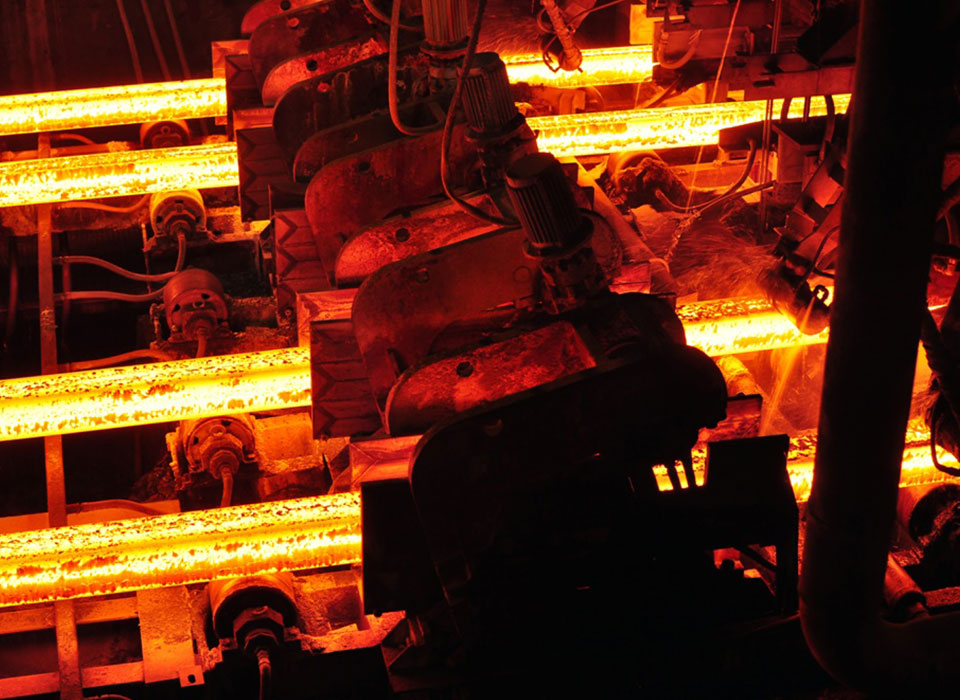
High Temperature Greases
BECHEM’s range for high temperature applications include greases developed from special Polyurea to advanced PTFE thickeners blended with synthetic as well as special mineral base oils.
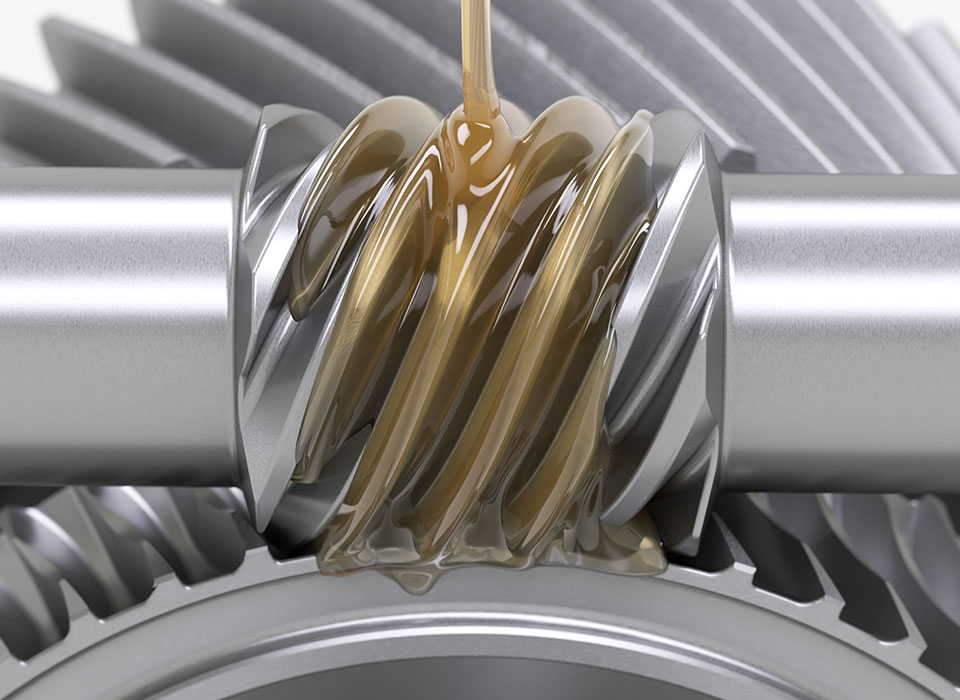
High Load Greases
BECHEM’s range of heavy duty greases formulated with high base oil viscosity and equipped with anti wear and EP additives ensure consistent, high strength lubricant film under boundary and mixed condition.