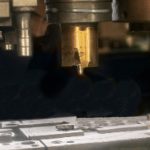
High Performance Grease for Effective Lubrication of Forging Press
March 12, 2024
Impact of high performance forming oil on metal shaving process
April 1, 2024Copper dust affecting surface finish and rejection rates in copper wire drawing process
Can industrial cleaners help increase surface finish, reduce wire breakage, improve machine cleanliness and avoid blackening in copper wire drawing process.
Industrial cleaners or degreasers play an integral role in efficiently removing tough dirt, grease, grime and other process chemicals from surface of machine components and finished products coming off the production line. Regular machine cleaning as a part of routine maintenance can create better work environment and in case of annealing process in wire drawing impact reject rates.
Selection of the appropriate cleaner or degreaser is critical as it may impact the effectiveness of the cleaning process, the health safety of the user and the overall performance of the equipment. Using an incompatible cleaning agent may damage or corrode the surface of metals, plastics or rubber.
The below case study illustrates how a suitable cleaner helped the customer get over the issues of blackening in copper wires and also help keep machine appearance in top shape.
Customer: An Indian wire and cable manufacturing giant, with production facilities in multiple locations and global supplies to diverse sectors.
Process: Copper wire drawing and annealing section.
Application details:
- Component: Dies and capstan in drawing machine
- Operation: Cleaning of machines and dies
- Machine: Ultrasonic
- Material: Metals, diamond, ceramics
Customer was using liquid fuels like petrol, diesel, methanol and detergents for cleaning. However wire finishing issues plagued the operations team with increased rejection rates.
Issues encountered by the operations team :
- Deposition of copper dust on surface of the wire before annealing process leading to rough surface finish
- Frequent breakage of wires resulting in production loss impacting productivity
- The copper wires turned black in the ‘drawing’ process, resulting in increased maintenance and delays in subsequent operations.
Observation by BECHEM team on causes for wire blackening and surface roughness of copper wires
- The copper wire being annealed developed surface roughness as a result of residues or other impurities being transferred to the metal due to the lack of cleaning in the annealing system.
- Cleaning of ‘die’ and ‘capstan’ are mandatory prior to the annealing process to get better slippage on the capstan.
- Poorly cleaned drawing section can trigger issues like wire breakage and uneven surface finish when the wire is drawn through a series of dies to produce the required form and thickness.
- Lack of cleanliness in the annealing section accelerated the rate of oxidation, leading to wire blackening
Understanding the requirement, the Bechem engineering team initiated a trial with the aqueous cleaner, Beruclean 3050.
Why Beruclean 3050?
- Heavy duty degreaser, Beruclean 3050 efficiently cleans tough greases, oils, drawing compounds and other process contaminants
- Suitable for metal surfaces like aluminium, steel, copper, bronze, ferrous etc. Beruclean 3050 can be safely used on machine surfaces with ceramic, plastic, rubber and painted materials as well
- Beruclean 3050 is effective for both traditional and modern cleaning techniques like ultrasonic washers, high pressure spray washer machine and spray washer machine, stream jet units and manual cleaning etc.
- Due to its low consumption, Beruclean 3050 is extremely cost effective.
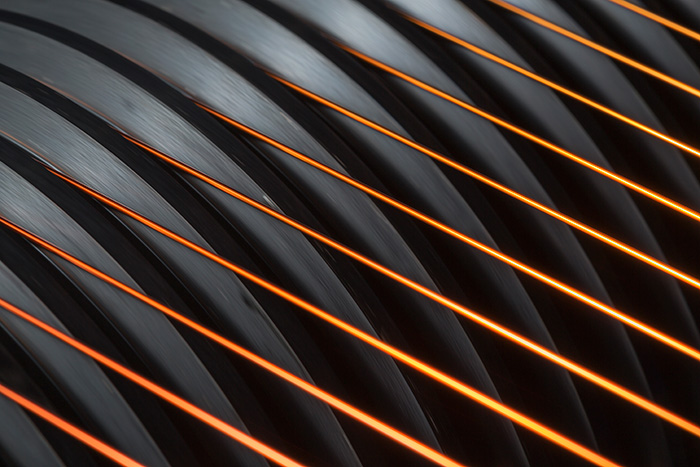
Trial observations:
- Excellent cleaning of machine components including capstan and die
- No traces of dust deposition were noted on the drawn wires. Superior surface finish of the copper wires was achieved
- No traces of corrosion or blackening observed. No lot was rejected during the trial period
- Clean equipment ensured cleaner working environment for the operations team
Observing the efficiency of the product in cleaning, the customer switched over to Beruclean 3050 fand proposed to explore other application areas and initiate the trial.
For more information on Bechem’s cleaner/degreaser, case studies and references write back to us at [email protected] or visit our website www.bechemindia.com
Support response: Median email response time of less than 3 hours.